In the world of fire safety and engineering, customized fire
performance testing devices play a crucial role. These devices are
designed to provide accurate and detailed information about how
materials, products, and systems respond to fire, enabling
industries to make informed decisions and ensure the highest levels
of safety.
The Customized Fire Performance Testing Devices are a suite of
advanced instruments that are specifically engineered to evaluate
the fire performance of a wide range of items. They serve the needs
of various sectors, including construction, manufacturing,
aerospace, and automotive. The primary goal is to determine
critical fire-related characteristics such as ignition resistance,
flame spread rate, heat release rate, smoke production, and the
toxicity of combustion by-products. By doing so, these devices
assist in product development, quality control, and compliance with
fire safety regulations.
- Durable and Heat-Resistant Construction
- These testing devices are built with high-quality materials that
can withstand the extreme conditions of fire testing. The frames
are typically made of heavy-duty stainless steel or alloy,
providing excellent structural integrity and resistance to heat
deformation. The interior chambers are lined with refractory
materials, capable of withstanding temperatures up to 1800°C. The
doors are designed with a double-layered, insulated structure and a
reliable sealing mechanism to prevent heat leakage and ensure the
accuracy of the test environment. A viewing window, made of
heat-strengthened glass or a transparent ceramic material, allows
for visual inspection during the test without compromising safety.
- Precision Temperature and Flame Control
- Temperature Control: The devices can precisely control the
temperature within the testing chamber. They can achieve a wide
temperature range, from ambient temperature to 1500°C, with an
accuracy of ±2°C. This is accomplished through a combination of
advanced heating elements, such as silicon carbide heaters, and a
sophisticated PID (Proportional-Integral-Derivative) control
system. Multiple thermocouples are strategically placed throughout
the chamber to ensure uniform temperature distribution and rapid
response to any temperature fluctuations. The user-friendly control
panel enables the programming of complex temperature profiles,
including ramping, holding, and cycling, to mimic different fire
scenarios.
- Flame Control: The flame generation system is highly adjustable. It
can produce flames with varying intensities, from a small pilot
flame to a high-powered, turbulent flame. The fuel supply and air
mixture can be precisely regulated, allowing for the customization
of flame characteristics such as heat output, shape, and color.
This is essential for testing the response of materials to
different types of fire exposure, such as the slow-burning flames
of a smoldering fire or the intense heat of a flashover.
- Advanced Instrumentation and Data Acquisition
- The testing devices are equipped with a comprehensive set of
sensors and measurement tools. In addition to temperature and flame
sensors, they include optical sensors for monitoring smoke density
and opacity. These sensors use light scattering or absorption
techniques to accurately measure the amount and density of smoke
produced. Gas sensors are also incorporated to detect and analyze
the composition of gases emitted during combustion, including toxic
gases such as carbon monoxide and volatile organic compounds. The
data acquisition system is a high-speed, multi-channel device that
records and stores all relevant data. It offers a sampling rate of
up to 10,000 samples per second, ensuring that even the most
transient changes in parameters are captured. The collected data
can be analyzed in real-time or retrieved later for in-depth
studies using specialized software, which provides detailed reports
and graphical representations of the test results.
- Versatile Testing Modes and Configurations
- These devices offer a variety of testing modes to accommodate
different sample types and testing requirements. They can perform
horizontal and vertical flame spread tests, where the behavior of a
material's surface as the flame travels across it is evaluated.
Cone calorimeter tests can be carried out to measure the heat
release rate and other combustion parameters of a sample under a
controlled radiant heat flux. Additionally, they can be configured
for fire resistance tests, such as testing the integrity of a
building component or a product enclosure under fire conditions.
The devices can also be integrated with other environmental control
systems, such as humidity and pressure control, to study the
combined effects of multiple factors on fire performance.
- Compliance with Industry Standards
- The Customized Fire Performance Testing Devices are designed to
comply with a wide range of international and national fire safety
standards. They adhere to ASTM (American Society for Testing and
Materials) standards, such as ASTM E84 for surface burning
characteristics, ASTM E1354 for heat and visible smoke release
rates, and ASTM E662 for smoke density. They also meet ISO
(International Organization for Standardization) standards,
including ISO 5660 for reaction-to-fire tests and ISO 1716 for
calorific value determination. This compliance ensures that the
test results are recognized and accepted by regulatory bodies and
industry peers, facilitating product certification and market
access.
- Chamber Size and Capacity
- The devices are available in different chamber sizes to suit
various sample sizes and testing volumes. Smaller chambers may have
interior dimensions of 0.3 meters x 0.3 meters x 0.3 meters,
suitable for testing small specimens or individual components.
Medium-sized chambers can measure 0.6 meters x 0.6 meters x 0.6
meters, providing enough space for testing larger samples or a
batch of products. Larger chambers, with dimensions exceeding 1
meter x 1 meter x 1 meter, are ideal for full-scale testing of
building materials or large industrial products. The interior
volume and shape are carefully designed to ensure proper air
circulation and uniform exposure of the sample to the fire and
environmental conditions.
- Temperature Range and Accuracy
- As mentioned earlier, the temperature can be controlled from
ambient to 1500°C, with an accuracy of ±2°C. The temperature ramp
rate can be adjusted from 0.5°C per minute to 100°C per minute,
allowing for the simulation of both slow and rapid temperature
changes. For example, a slow ramp rate may be used to study the
thermal degradation of a material over time, while a rapid ramp
rate can mimic the sudden heat increase during a fire outbreak.
- Flame Intensity and Control Parameters
- The flame intensity can be adjusted over a wide range, with a
maximum heat output equivalent to several megawatts per square
meter. The fuel flow rate can be varied from a few milliliters per
minute to several liters per minute, and the air-fuel ratio can be
precisely controlled within a range of 1:1 to 20:1. These
parameters enable the creation of flames with different
characteristics, from a small, stable flame for precision testing
to a large, turbulent flame for more severe fire simulations.
- Data Acquisition Rate and Resolution
- The data acquisition system samples sensor data at a rate of 10,000
samples per second. The temperature sensor has a resolution of
0.1°C, the smoke density sensor can detect changes as small as
0.005% opacity, and the gas sensors have a sensitivity in the parts
per million (ppm) range for most common gases. This high-resolution
and high-speed data capture ensure that the devices provide
detailed and accurate information about the fire performance of the
tested samples.
- Compliance with Key Fire Testing Standards
- The devices comply with ASTM E84, ASTM E1354, ASTM E662, ISO 5660,
and ISO 1716, among other relevant standards. They can also be
customized to meet specific requirements of other industry
standards or regulatory codes, ensuring their adaptability to
different industries and applications.
- Accurate Simulation of Fire Scenarios
- The primary function of these devices is to provide a highly
accurate and realistic simulation of fire conditions. By precisely
controlling temperature, flame characteristics, and other
environmental factors, they allow for the comprehensive evaluation
of how materials and products will behave in an actual fire. For
example, they can determine if a building material will contribute
to the spread of fire, if a product will release toxic gases that
could endanger occupants, or if a component will maintain its
structural integrity under fire exposure. This information is
invaluable for architects, engineers, and product designers to make
informed decisions and develop safer and more fire-resistant
designs.
- Enhanced Product Development and Quality Assurance
- Through comprehensive fire performance testing, manufacturers can
identify and address potential fire safety issues in their
products. If a material shows a high flame spread rate or excessive
smoke and toxic gas production, appropriate modifications can be
made, such as adding fire retardants, changing the material
composition, or improving the product's design. This leads to the
development of higher-quality and more reliable products that meet
or exceed fire safety standards. The devices also serve as a
crucial part of quality control, ensuring that each batch of
products is tested and compliant, thereby reducing the risk of
product recalls and enhancing brand reputation.
- Facilitation of Regulatory Compliance and Certification
- Regulatory bodies rely on accurate and standardized fire test
results to enforce fire safety regulations. The Customized Fire
Performance Testing Devices enable manufacturers to conduct tests
in accordance with recognized industry standards, providing the
necessary data for regulatory compliance and product certification.
This helps in streamlining the approval process, ensuring that
products can be legally marketed and used in various applications,
from residential and commercial buildings to industrial facilities
and transportation vehicles.
- Stringent Manufacturing Process
- The fire performance testing devices are manufactured under strict
quality control procedures. Each component, from the heating
elements and sensors to the control panel and chamber lining, is
carefully sourced and inspected for quality and performance. The
assembly process is carried out by highly trained technicians in a
clean and controlled environment. The devices undergo a series of
calibration and validation tests during the manufacturing process
to ensure that they meet the required accuracy and performance
standards.
- The calibration of temperature, flame, and other sensors is a
critical part of the manufacturing process. It is performed using
traceable reference standards that are calibrated to the highest
levels of accuracy, guaranteeing the reproducibility of the test
results. Rigorous quality audits and inspections are conducted at
various stages of production to maintain the highest level of
product quality and compliance with fire safety standards.
- Quality Certification and Validation
Our devices have obtained relevant quality certifications and have
been validated by independent fire testing laboratories. They have
been proven to provide accurate and reliable test results,
conforming to the relevant industry standards. We also continuously
update and improve our product based on the latest technological
advancements and customer feedback from the fire safety industry to
ensure its long-term performance and compliance.
- Construction Industry
- A leading construction materials manufacturer used the Customized
Fire Performance Testing Devices to test a new type of flooring
material. The tests revealed that the material had excellent fire
resistance, with a low flame spread rate and minimal smoke
production. This enabled the company to market the material as a
high-performance, fire-safe flooring option, meeting the demands of
architects and building owners for safer construction materials.
- A construction firm tested different types of wall panels in the
devices. The results showed that one particular panel had a higher
heat release rate than expected, which could pose a fire hazard. By
using a different core material and retesting, they were able to
ensure the fire safety of their building projects and comply with
building codes.
- Manufacturing Sector
- An electronics manufacturer tested the fire performance of their
circuit boards. The testing identified that certain components on
the circuit boards released toxic gases when exposed to fire. By
redesigning the circuit boards and using fire-retardant components
and coatings, they were able to produce circuit boards that met
fire safety standards and reduced the potential risk to consumers
in case of a fire.
- A furniture manufacturer used the devices to evaluate the fire
resistance of their upholstery fabrics. The tests showed that some
fabrics had a rapid flame spread, which could be dangerous in a
domestic or commercial setting. By using fire-retardant-treated
fabrics and testing them again, they were able to improve the fire
safety of their furniture products and gain a competitive edge in
the market.
- Aerospace and Automotive Industries
- An aerospace company tested the fire resistance of a new composite
material for use in aircraft interiors. The Customized Fire
Performance Testing Devices allowed them to simulate the extreme
conditions of a cabin fire, including high temperatures, rapid
temperature changes, and the presence of oxygen. The results helped
them optimize the material's composition and design, ensuring the
safety of passengers and crew in the event of a fire.
- An automotive manufacturer tested the fire behavior of different
wiring harnesses. The testing identified potential weak points in
the harness design, such as areas where the insulation could melt
and cause a short circuit. By redesigning the harness and using
fire-resistant materials, they were able to improve the fire safety
of their vehicles and reduce the risk of electrical fires.

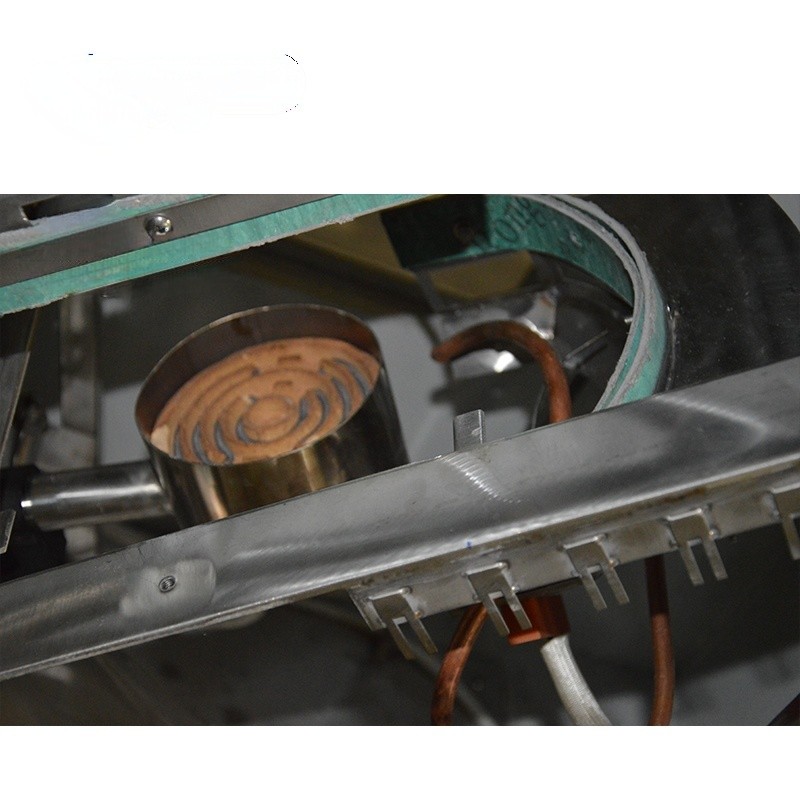
- Pre-Sales Technical Consultation
Our team of fire safety experts provides in-depth technical
consultations to help customers understand the capabilities and
suitability of the Customized Fire Performance Testing Devices for
their specific testing needs. We offer demonstrations and training,
tailored to the fire safety industry, to familiarize customers with
the operation and functionality of the equipment before purchase.
We also assist in selecting the appropriate test methods and
accessories based on the materials or products to be tested. - After-Sales Service and Maintenance
We offer comprehensive after-sales service, including on-site
installation and commissioning. Our technicians are available for
regular maintenance, calibration, and emergency repairs. We provide
spare parts and upgrades to keep the test devices operating at peak
performance. We also offer service contracts that include
preventive maintenance and priority technical support, ensuring the
long-term reliability and availability of the equipment for fire
performance testing. - Training and Technical Support
We conduct training programs for new users to ensure they can
effectively operate the Customized Fire Performance Testing Devices
and interpret the test results. Our technical support team is
available 24/7 to answer questions, provide troubleshooting
assistance, and offer guidance on test method optimization and
compliance with fire safety standards. We also provide software
updates and support for the data acquisition and analysis systems,
enabling customers to take full advantage of the latest features
and technologies in fire performance testing.
The Customized Fire Performance Testing Devices are an essential
asset for any organization involved in fire safety testing and
product development. If you are looking to enhance your fire
testing capabilities, ensure compliance with industry standards, or
drive innovation in fire safety, this is the ideal solution.
Contact us today to learn more and get a customized quotation. Let
us help you unlock the full potential of your fire safety testing
and product quality assurance.