In the realm of electronics and industrial manufacturing, the need
for components to withstand harsh environmental conditions is of
paramount importance. The Custom Thermal Shock Chambers, designed
to meet the IEC-60068-2-14, Test Na² test standards, emerge as a
crucial asset in evaluating and enhancing the durability of a wide
range of products.
This custom-built thermal shock chamber is dedicated to subjecting
components and products to the specific thermal shock testing
requirements outlined in the IEC-60068-2-14, Test Na² standard. It
serves industries such as automotive, aerospace,
telecommunications, and consumer electronics. The primary goal is
to assess the ability of components like circuit boards,
connectors, sensors, and housings to endure rapid and extreme
temperature fluctuations. By replicating the thermal shock
scenarios that these components may encounter during their
operational lifetimes, manufacturers can identify potential
weaknesses, optimize design and manufacturing processes, and ensure
the reliability and performance of their products in diverse and
challenging environments.
- Robust and Insulated Chamber Structure
- The chamber is constructed with heavy-duty, heat-resistant
materials that can withstand the intense thermal stresses. The
walls are made of high-strength steel alloy, combined with advanced
thermal insulation layers to minimize heat transfer between the hot
and cold zones. The door is engineered with a reliable sealing
mechanism and a viewing window, allowing operators to monitor the
testing process without compromising the chamber's integrity. The
interior is designed with adjustable racks and fixtures, enabling
the accommodation of variously sized and shaped components and
ensuring uniform exposure to the thermal shock conditions.
- Precision Temperature Control System
- Temperature Range and Cycling: Capable of achieving a wide
temperature range, typically from -60°C to +150°C. The system can
execute rapid temperature cycling between the hot and cold zones,
with a transition time as short as a few seconds. This is essential
for mimicking the abrupt temperature changes that components may
experience in real-world applications, such as when a device is
powered on or off, or when exposed to external heat sources. The
temperature control is accurate to within ±0.3°C, providing
reliable and repeatable test results.
- Intuitive Control Panel and Data Acquisition Interface
- The control panel is designed for user-friendliness, allowing
operators to easily set and adjust test parameters such as
temperature levels, dwell times in each zone, and the number of
thermal shock cycles. It provides real-time displays of the current
temperature in both zones, the status of the testing process, and
any alarms or warnings. The chamber is integrated with a
comprehensive data acquisition system that records all relevant
test data. This includes temperature histories, cycle times, and
any observable changes in the physical, electrical, or mechanical
properties of the components. The data can be stored in a built-in
memory or exported to external storage devices for further
analysis. The system can also generate detailed test reports in
various formats.
- Safety Features and Alarms
- To ensure the safety of operators and the protection of the test
samples and the chamber itself, a range of safety features is
incorporated. These include over-temperature and over-current
protection systems, emergency stop buttons, and alarms for abnormal
temperature fluctuations, equipment malfunctions, or any other
safety-related issues. The chamber is also equipped with proper
ventilation and exhaust systems to handle any potentially harmful
gases or vapors that may be generated during the testing process.
- Temperature Range and Accuracy
- The -60°C to +150°C temperature range with ±0.3°C accuracy offers a
comprehensive testing spectrum. Different components have different
temperature tolerances and performance characteristics. For
example, electronic components may experience changes in electrical
conductivity or mechanical stress at extreme temperatures. The
accurate temperature control ensures that the test conditions are
precisely maintained, allowing for a detailed assessment of
component behavior.
- Thermal Shock Cycle Parameters
- The chamber can be programmed to perform a specific number of
thermal shock cycles, typically ranging from 10 to 500, depending
on the requirements of the IEC-60068-2-14, Test Na² standard and
the nature of the components. The dwell time in each temperature
zone can also be adjusted, from a few minutes to several hours.
This flexibility enables manufacturers to simulate a wide variety
of real-world scenarios and evaluate the long-term durability of
components under different thermal shock conditions.
- Testing Volume and Payload Capacity
- The chamber offers a customizable testing volume, usually ranging
from 2 m³ to 10 m³, to accommodate a significant number of
components. The payload capacity is designed to handle heavy and
bulky components, with a maximum capacity of up to several tons.
This allows for the testing of both individual components and small
assemblies.
- Data Sampling Frequency and Resolution
- The data acquisition system samples data at a frequency of up to
600 Hz. The temperature data has a resolution of 0.1°C. This
high-resolution and frequent sampling enable the detection of even
the slightest temperature changes and trends, providing valuable
insights into the behavior of the components during thermal shock
testing.
- Accurate Simulation of IEC-60068-2-14, Test Na² Test Conditions
- The chamber replicates the exact thermal shock conditions specified
in the IEC-60068-2-14, Test Na² standard. This is crucial as
components must meet these requirements to ensure their compliance
and reliability. By subjecting the components to these precise
simulations, manufacturers can be confident that their products
will perform as expected in real-world applications.
- Product Design Optimization and Quality Control
- Through a series of tests on different component prototypes, the
data obtained from the chamber can be used to optimize product
designs. Engineers can analyze the performance of various
materials, geometries, and manufacturing techniques under thermal
shock stress. The chamber also serves as a vital tool for quality
control, ensuring that each production batch of components meets
the required standards. For example, if a particular connector
shows signs of loosening after a certain number of thermal shock
cycles, the design or manufacturing process can be adjusted to
correct the issue.
- Research and Development Support
- In the field of component research and development, the Custom
Thermal Shock Chambers offer valuable insights. Researchers can use
them to study the fundamental properties of new materials and their
interactions with thermal shock. They can explore innovative
designs and technologies that result in more resilient components.
For instance, materials scientists can test the performance of
novel composites or advanced heat sinks under IEC-60068-2-14, Test
Na² test conditions, using the chamber to evaluate their potential
for future applications.
- Compliance Testing and Certification
- The equipment is essential for conducting compliance testing to
meet the IEC-60068-2-14, Test Na² standard. The electronics and
manufacturing industries have strict regulations regarding
component performance, and the test results obtained from the
chamber can be used to certify that the components meet these
standards. This is crucial for market acceptance and for ensuring
the overall safety and reliability of products.
- Stringent Manufacturing Process
- The Custom Thermal Shock Chambers for IEC-60068-2-14, Test Na² are
manufactured under strict quality control procedures. Each
component, from the chamber structure and insulation materials to
the temperature control unit and safety features, is sourced from
reliable suppliers and undergoes thorough inspection and testing.
The assembly process is carried out by highly trained technicians
in a clean and controlled environment. The chamber is calibrated
and verified at multiple stages during production to ensure its
accuracy and performance.
- Quality Certification and Validation
Our chamber has obtained relevant quality certifications and has
been validated by independent testing laboratories. It has been
proven to provide accurate and reliable test results, conforming to
the IEC-60068-2-14, Test Na² standard and other international and
national testing standards. We also continuously update and improve
our product based on the latest technological advancements and
customer feedback from the industries to ensure its long-term
performance and compliance.
- Automotive Component Testing
- An automotive manufacturer used the chamber to test the electronic
control units (ECUs) of a new vehicle model. The ECUs were
subjected to a series of thermal shock cycles, simulating the
temperature changes that occur during engine start-up, normal
driving, and extreme weather conditions. The testing revealed a
potential issue with the soldering joints of a certain component on
the ECU board. By improving the soldering process and using a more
temperature-resistant solder material, the manufacturer was able to
enhance the reliability of the ECUs and reduce the risk of
in-vehicle system failures.
- Aerospace Equipment Evaluation
- An aerospace company evaluated the performance of a new sensor used
in an aircraft's navigation system. The sensor was exposed to
extreme temperature transitions, replicating the conditions from
high-altitude flight to ground operations. The results showed that
the sensor's calibration drifted under thermal shock. By
redesigning the sensor's calibration algorithm and using a more
stable sensor housing material, the company was able to improve the
accuracy and reliability of the navigation system, ensuring safer
flights.
- Telecommunications Device Durability Testing
- A telecommunications equipment manufacturer tested their base
station transceiver units in the chamber. The units were subjected
to thermal shock cycles to assess their durability and performance.
The testing identified a weakness in the cooling system's heat
exchanger, which caused overheating after repeated thermal shock.
By optimizing the heat exchanger design and using a more efficient
cooling fan, the manufacturer was able to increase the transceiver
units' reliability and reduce maintenance requirements.

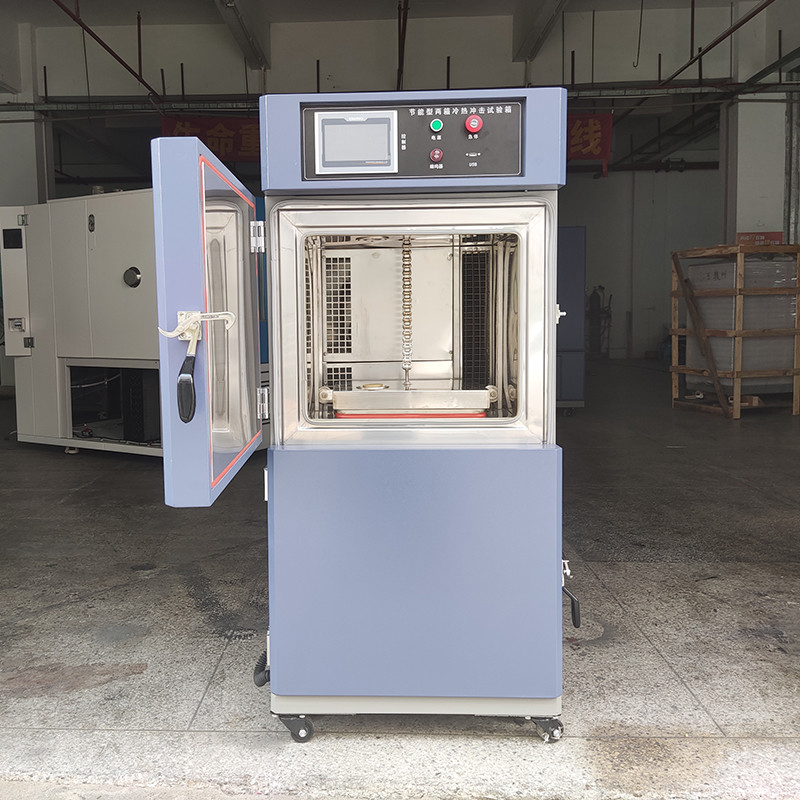
- Pre-Sales Technical Consultation
Our team of testing experts provides in-depth technical
consultations to help customers understand the capabilities and
suitability of the chamber for their specific testing needs. We
offer demonstrations and training, tailored to the relevant
industry, to familiarize their engineers and technicians with the
operation and functionality of the chamber before purchase. We also
assist in selecting the appropriate test parameters and accessories
based on the components to be tested. - After-Sales Service and Maintenance
We offer comprehensive after-sales service, including on-site
installation and commissioning. Our technicians are available for
regular maintenance, calibration, and emergency repairs. We provide
spare parts and upgrades to keep the chamber operating at peak
performance. We also offer service contracts that include
preventive maintenance and priority technical support, ensuring the
long-term reliability and availability of the tester for
IEC-60068-2-14, Test Na² thermal shock testing of components. - Training and Technical Support
We conduct training programs for new users to ensure they can
effectively operate the Custom Thermal Shock Chambers and interpret
the test results. Our technical support team is available 24/7 to
answer questions, provide troubleshooting assistance, and offer
guidance on test method optimization and compliance with
IEC-60068-2-14, Test Na² and other industry testing standards. We
also provide software updates and support for the data acquisition
and analysis systems, enabling customers to take full advantage of
the latest features and technologies in testing.
The Custom Thermal Shock Chambers that meet the IEC-60068-2-14,
Test Na² test standards are an essential asset for any organization
involved in component testing and development. If you are looking
to enhance your testing capabilities, ensure compliance with
industry standards, or drive innovation in product design, this is
the ideal solution. Contact us today to learn more and get a
customized quotation. Let us help you unlock the full potential of
your component testing efforts.